Serenco uses cookies on its website, to improve your experience on our website. More information about this can be found in our privacy statement. By using our website, you agree to the use of these cookies.
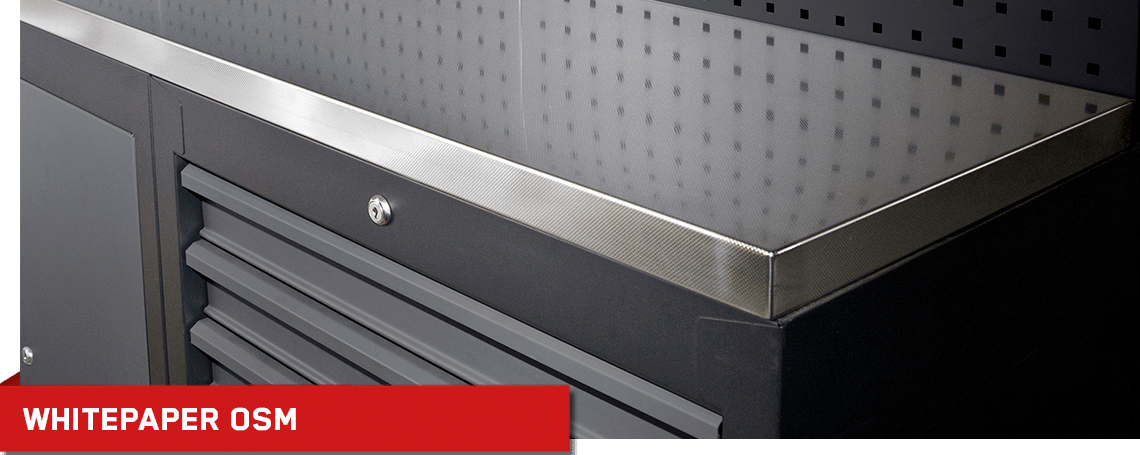
Find all information on modular workshop equipment here.
Tips on the purchasing process of a modular workshop equipment system.
In recent years, the needs and requirements for workshop equipment have changed considerably. As a result, organized storage systems are increasingly being chosen. In addition to the storage of normal hand tools, there is also plenty of room to store all other tools and materials in a fixed place and, if desired, under lock and key.
The purchase of such a workshop equipment system isn’t always straight-forward. Since it is often a considerable investment, I have, with my extensive practical experience, set up a step-by-step plan for you. So that you make the important decisions in the right order and don't forget anything
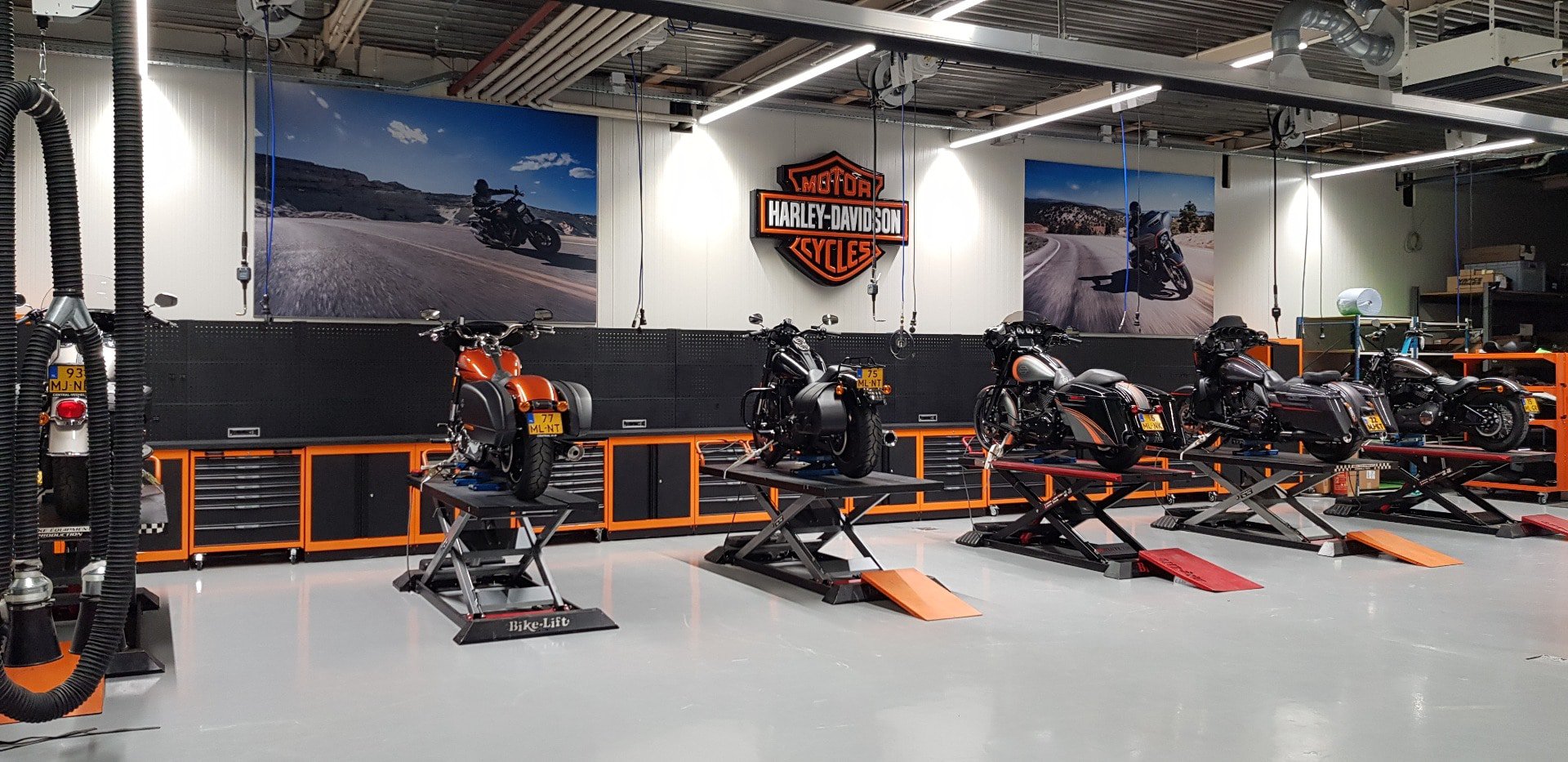
1/ Where will the setup be placed?
It is very important that the setup is designed well in order for it to match the available space. So that a spacious, safe and easily accessible workplace is created. With enough space to work pleasantly and comfortably throughout the day.
2/ Choose the desired depth of the worktops (500 or 700mm)
This depends on the available space (see 1) and the nature of the work. Especially if larger jobs are regularly performed on the workbench, it is desirable to have the space (= 70cm). If at least enough space is available for this.
3/ Keep the worktop height in mind.
In regards with "ergonomic" work and all that comes with it. The ideal working height at a workbench is 5 inches above the elbows. Try to get as close to that as possible. And of course, the setup is height adjustable so that further adjustments can be made in the future.
4/ Choose the desired worktop type.
Where appearance, abrasion resistance and ease of cleaning come into play. For many "heavy duty" jobs, stainless steel seems to be the obvious choice. Wood has by far the warmest appearance. And plywood is the choice when it comes to no nonsense and value for money.
5/ Estimate the distribution of desired shelf space (low and high cabinets)
Pretty tricky, but nice not to have to order extra shelves afterwards. The best way to do this is to lay out the appropriate items on the workshop floor. You then have a good overview and can -if desired- immediately determine the layout + throw away unnecessary items..
6/ Make a good estimate of the desired hanging area (mostly for special tools) and the portion that is to be stored behind lock & key.
Just as before, try to make a good estimate in advance to avoid disappointment afterwards. Special tools are very expensive and it is important to handle them with extra care. Again, displaying them on the floor can help. Also consider storing some of these special tools in a locked room. Not the cheapest solution, but this will undoubtedly pay for itself in the long run.
7/ Estimate the ideal filling of the drawers.
This largely determines the ease of work and efficiency. Try to assess this as well as you can and take the trouble to put things away very carefully the first time. In most cases the drawers are first filled with a basic set of hand tools, supplemented by the more tailor-made tool foams. The drawers that remain can be filled with trays, compartments and boxes as you see fit, in any size. Or with just a thin foam mat if loose tool items will be placed inside.
8/ Keep in mind the maximum load capacity of shelves and the load capacity of drawers.
Check that these values match your desired weights. Modular workshop equipment lasts a very long time. At least if you fit it properly. And an important part of that is to not overload the materials, in this case the shelves and drawers. That increases wear and tear and subsequently decreases the lifespan.
9/ Determine if there is a need for power or data connections, and if so, how many and where?
A part of workplace design that will play an increasingly important role. Who is going to use where and what? Normal power points, USB power points and any network cables? By properly mapping this out in the preliminary stage, you will greatly benefit from it in the follow-up stage.
10/ Determine if there is a need for integrated air, electrical or water hose hoses
Formerly mostly mounted separately on the wall. But so much nicer and more efficient to integrate directly into workshop furniture. Relatively easy to include in the initial installation of workshop furniture and a much more complicated and costly process afterwards.
11/ Decide whether trash containers will be integrated into the modules.
Garbage containers are not exactly pretty to look at and take up a relatively large amount of space. While the standard container size does not always match the actual need. Hence, it is advisable to think about this in advance and estimate what can be integrated into the workshop layout.
12/ Determine if there is a need for an integrated sink and/or sinks.
In some workplaces, the distance from some workstations to the restroom is long. This is not always efficient. Consider the walking distance and the distractions associated with it. It can also be very nice to have a sink within easy reach in the event of an emergency.
13/ Inventory the lighting needs of the set(s)
Good lighting is half the battle. Especially in complicated repairs. Incorporate this issue directly into your workshop design. So a good lighting plan. Easy to assemble when you first assemble your workshop equipment.
14/ Decide whether you want the installation done yourself or by the supplier.
The supplier's installation crew is very knowledgeable and will undoubtedly do the installation a little faster for that reason. But there are costs involved. Doing it yourself is also an option, it is usually not very complicated, but obviously takes a little longer.
15/ Find one or more vendors that can meet all of the above requirements.
In regards to the story above, you have gathered that there is a lot to keep in mind when purchasing such tailor made workshop equipment. In that respect, it is quite complex with considerable amounts of money involved. It is nice to be well advised and to spar with someone who knows the supplier's product range like the back of their hand. This makes the purchasing process much more efficient and pleasant.
I sincerely hope that I have helped you quite a bit with this. Should you still have additional questions, please contact me directly. You can find the phone number on the Serenco Netherlands website.
Serenco Nederland / BOXO Europe / Anton van Zijtveld
Utrecht January 11th 2023
Download whitepaper
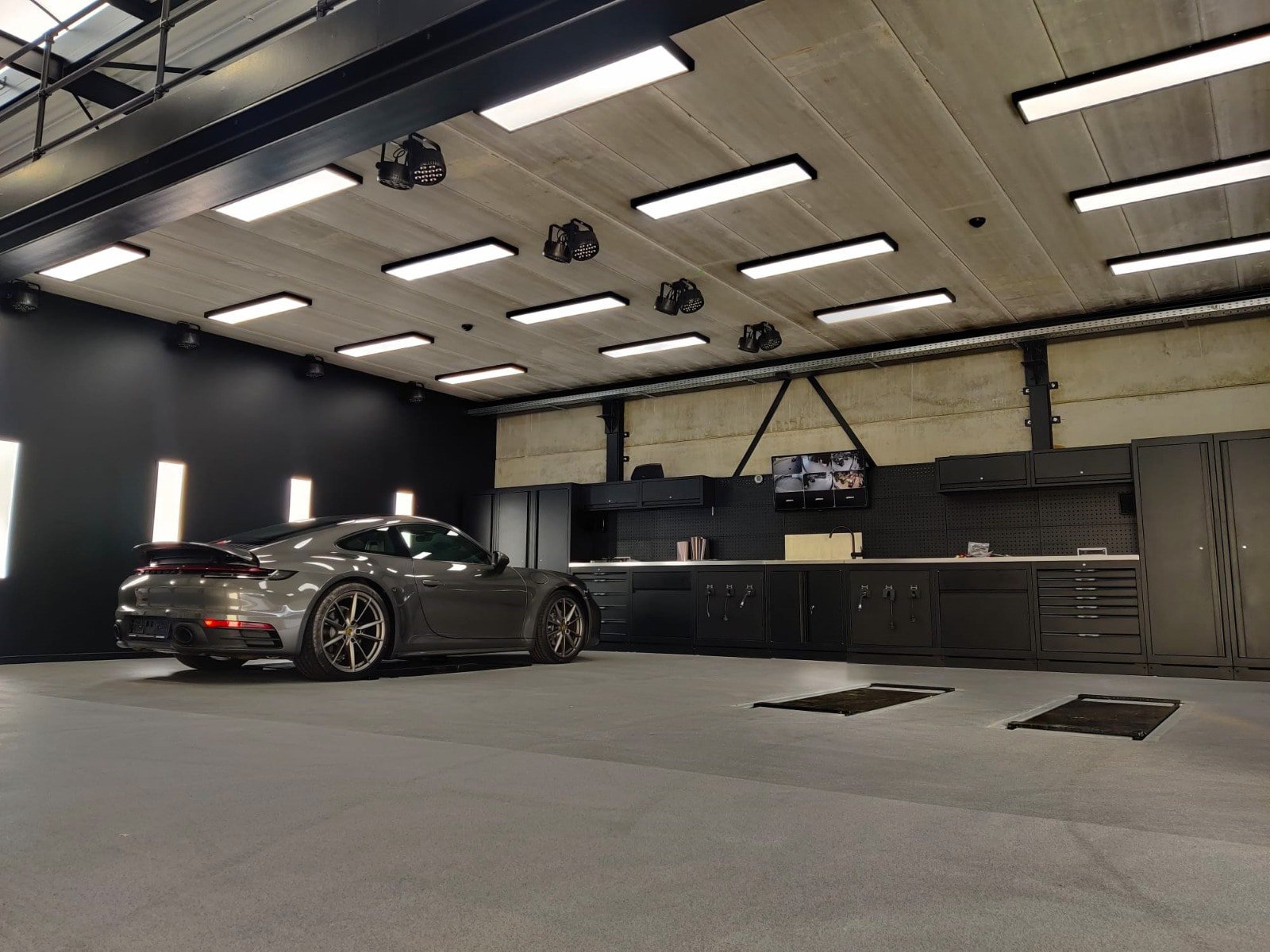